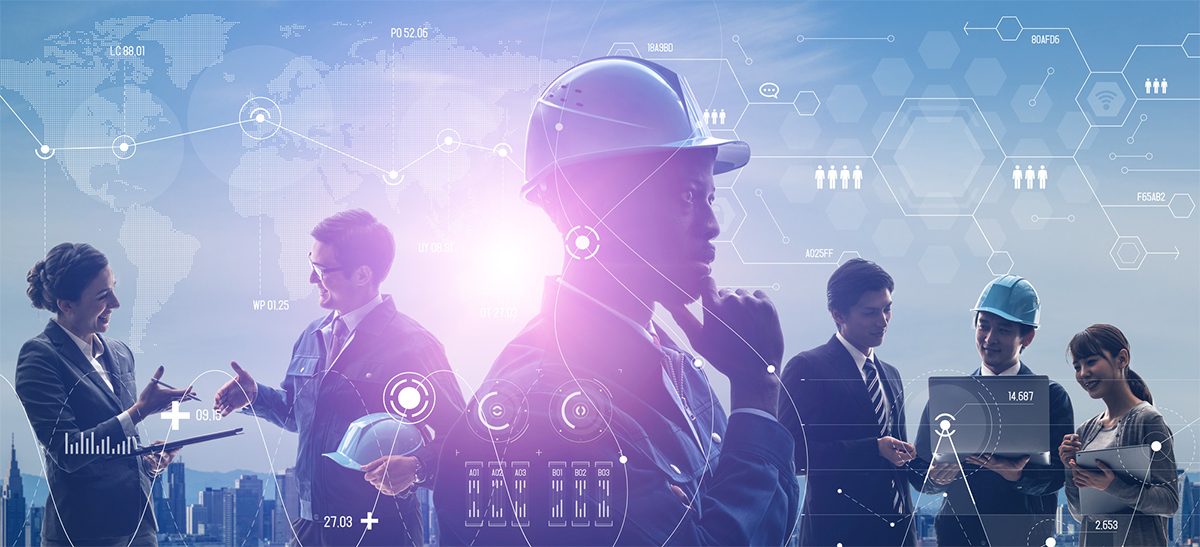
製造業のデジタルトランスフォーメーション(DX)や、工場を情報システムと連携させながら自動化する「スマートファクトリー」の取り組みが大きな注目を集めています。しかし、中小の製造業にとっては、こうした「スマートものづくり」の実現はかなりハードルが高いと感じる方もいらっしゃるのではないでしょうか。ここでは、日本能率協会コンサルティング(JMAC)で、製造業のDXやスマートものづくりのコンサルティング支援に取り組む小野甫氏(デジタルイノベーション事業本部 AI・IoT推進室 室長)と神山洋輔氏(デジタルイノベーション事業本部 スマートファクトリー推進室 室長)に、DX・スマート化を成功させる秘訣について伺いました。
スマートものづくりとは何か
「製造業のDX」や「スマートものづくり」を端的に言うと、「デジタル技術を使って今までのものづくりのやり方を変革し、企業の競争力を高めること」です。もう少しかみ砕いて言うと、デジタル技術によって、QCD(Quality、Cost、Delivery)の改善や製品の付加価値の向上といった製造業の課題を解決することです。
具体的には、生産性向上や納期短縮などのために、いろいろな製造設備や機器をネットワークでつなげることでデジタルデータを収集・分析して製造現場の様々な状況を見える化したり、ロボットや3Dプリンターを導入したりと、様々なスマートものづくりの事例があります。
最近では、生産ラインにAIを活用したり、生産ラインの集中管理システムであるMES(Manufacturing Execution System)と連携させたりする先端事例や、需要動向に直結したマスカスタマイゼーションができる「スマートファクトリー」の報告も出てきています。
実は、こうしたスマートものづくりの概念自体は昔からあり、1980年代のFA(Factory Automation)とかCIM(Computer Integrated Manufacturing)などの延長と言えます。当時は技術基盤が十分ではなかったためコンセプトだったものが、今ではインターネットの普及やデジタル技術の進化、低コスト化によってかなりのところまで実現できるようになってきています。
ものづくりのDX・スマート化は
3つの階層で考える
今、ものづくりの現場では、3つの階層でDXやスマート化が進められています。これを、日本能率協会コンサルティングでは「イノベーションカテゴリトライアングル」と呼んでいます。3つの階層というのは、(Ⅰ)「課題解決領域」、(Ⅱ)「最適化領域」、(Ⅲ)「価値創造領域」です。
1つ目の階層、つまり図のトライアングルで1番下にある階層の「課題解決領域」では、IoTやITを使って、製造現場の改善や生産性の向上を行います。例えば、工場の生産ラインで働く人や工場内の搬送車の導線を見える化して作業効率を図ったり、ウェアラブル端末を使って生産ラインにおける部品のピッキングミスをなくしたりする改善です。
2つ目の「最適化領域」は、こうした生産現場の課題を一つずつ解決していこうというものではなく、工場全体を全自動化する試みや、さらにスマート化の適用範囲を広げて生産から販売までのサプライチェーン全体を情報システムで一気通貫的につなぎ自動化・最適化を進めていこうという取り組みです。一般に、メディアでよく取り上げられる「スマートファクトリー」やドイツで提唱されている「インダストリー4.0」の先進事例はこの階層でのDX・スマート化になります。
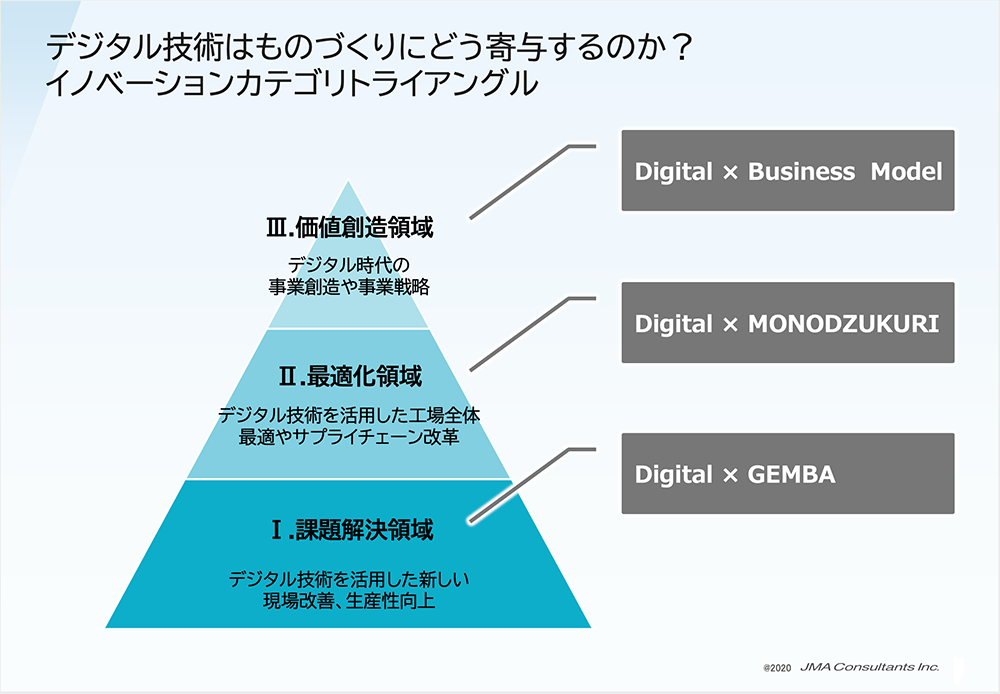
ものづくりのDX、スマート化は3つの階層で行われている。約7割の製造業が、(Ⅰ)の「課題解決領域」、つまり「現場の改善」のDX・スマート化を進めている
(図提供:日本能率協会コンサルティング、以下JMAC)
3つ目の「価値創造領域」は、デジタル技術によって企業のビジネスモデルそのものを変革したり、全く新しいビジネスを創造したりするような話です。例えば、製品の製造・販売がメインだった製造業の会社が、クラウドを使うことによって顧客に販売した製品のその後の状態をリアルタイムでモニタリングするアフターサービスのビジネスを生み出すようなケースです。場合によっては製造業だった企業がサービス業へと事業構造や業種・業態を変えることにもつながります。
世間で行われているものづくり企業のDX・スマート化は、この3領域のうち(Ⅰ)(Ⅱ)の領域に集中しています。JMACがクライアント企業にアンケート調査をした結果では、製造業の7割ほどが生産現場のデジタル改善に取り組み、5割弱が工場やスマートチェーン全体の最適化に取り組んでいます。(Ⅲ)の領域に手を付けている会社は一部の大手企業を除いてまだ少ないというのが現状です。
つまり、多くの中小ものづくり企業にとっての「スマートものづくり」とは、「課題解決領域」のDX・スマート化であり、デジタル技術・デジタルツールを使って、自社の生産現場の改善と生産性向上を目指すことと言ってもいいでしょう。
ここからは、こうした生産現場のDX・スマート化に絞り、成功している企業に共通する考え方・やり方を紹介します。
製造現場のDXを成功させる
5つのポイント
現場のDX・スマート化を成功させるポイントは大きく5つあります。「ローコスト」「スモールスタート」「レトロフィット」「ハンドメイド」「アップデート」です。
最初の3つは、簡単に言えば「小さい範囲で、安く、古い設備のことも考えて始める」ということ。大企業に比べると豊富な資金源を持たず、人材も少ない中小の製造業にとっては極めて重要な考え方です。日々、生産している製造の現場に、いきなり大きく新しい仕組みを入れようとしても現場担当者としてはなかなか受け入れがたいでしょう。
また、多くの中小企業では、長年使い続けている古い設備が今も現役で稼働しています。古い設備にも適用できるようなDX・スマート化を考えるとよいでしょう。例えば、稼働率を見える化するような場合に、デジタル・インターフェースのある新しい設備を導入してPLC(Programmable Logic Controller)による制御をしようとするのではなく、安く手に入る温度センサーや光センサーを使って古い設備のままでも稼働率の見える化ができます。こういう「レトロフィット」の考え方が大切になってきます。
残り2つは「手作り感のある改革」と「トライ&エラー」です。ものづくりの現場には、生産ラインの設備や機械・装置を「いじることが好きな人たち」が必ずいます。こうした設備や機械のことを熟知していて、古い設備の修理や保全・改修が上手にできる人たちが自分たちの手で触れ、改善活動の一環としてトライ&エラーをしながらDX・スマート化できるようなやり方・仕組みにすることです。
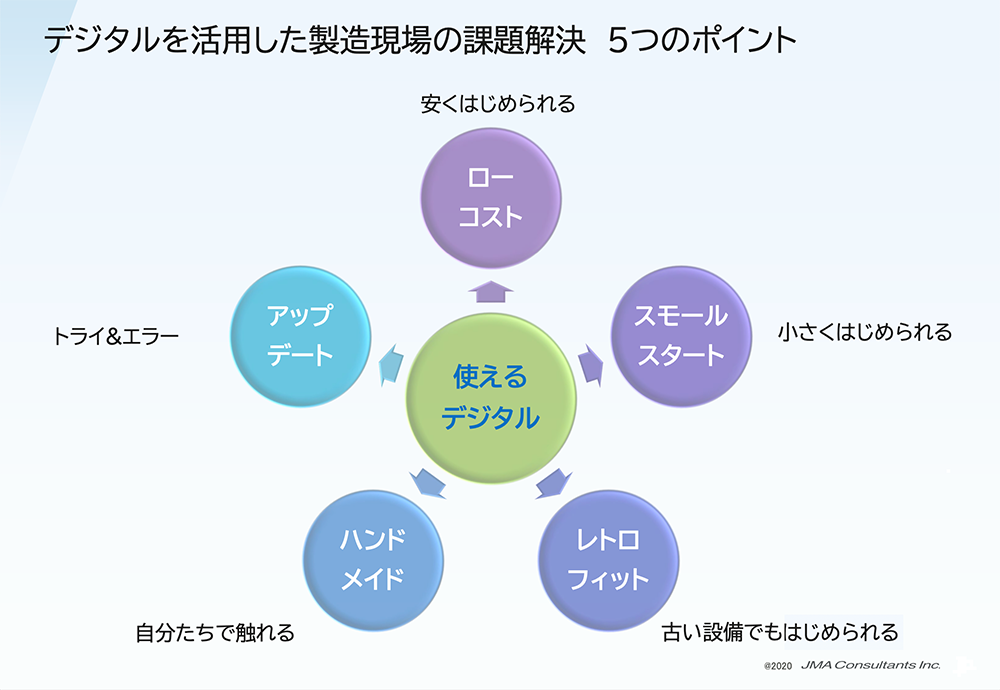
ものづくりの現場でDX・スマート化を成功させるための5つのポイント。安く、小さく、古い機械でもできるようにスタートさせ、現場が自分たちで設備・装置を改修しながら、トライ&エラーで改善を進められるようにすることが重要
(図提供:JMAC)
どこから手をつければいいか
わからない場合は?
規模の小さな企業の場合、自社の製造工程の中で、どの部分をDX・スマート化すべきかよくわからないケースが見受けられます。こうした場合には、製造現場で必要な7つの情報について整理しながら見ていくと有効な手がかりが得られます。図に示したのはJMACの「IoT7つ道具」。つまり、製造現場で重要な7つの情報です。
7つの情報というのは、
- 人や機器の「位置」(Location)
- 人の動きを示す「作業」(Operation)
- よく発生する問題の「場面」(Situation)
- 稼働率や故障頻度を示す「稼働」(Availability)
- 生産量や投入量などの「数量」(Count)
- 製品や仕掛品の「品質」(Quality)
- 作業の安全に関する「危険」(Hazard)
です。
DX・スマート化を考える際には、この7つの切り口ごとに、生産現場の困りごとや改善したいことを考えていくと、何をDX・スマート化すべきかが見えてきます。
この時に、あくまでも目的思考で考えることが大切です。デジタルツールありきで「あのツールを導入したい」からアプローチをすると失敗しがちです。まず、現場の困りごとや改善したいことをみつけ、何を実現したいのか、何故それが必要なのかをきっちり固めてから、それを実現するデジタル技術やツールを選ぶという順番でDX・スマート化を進めることが必要です。
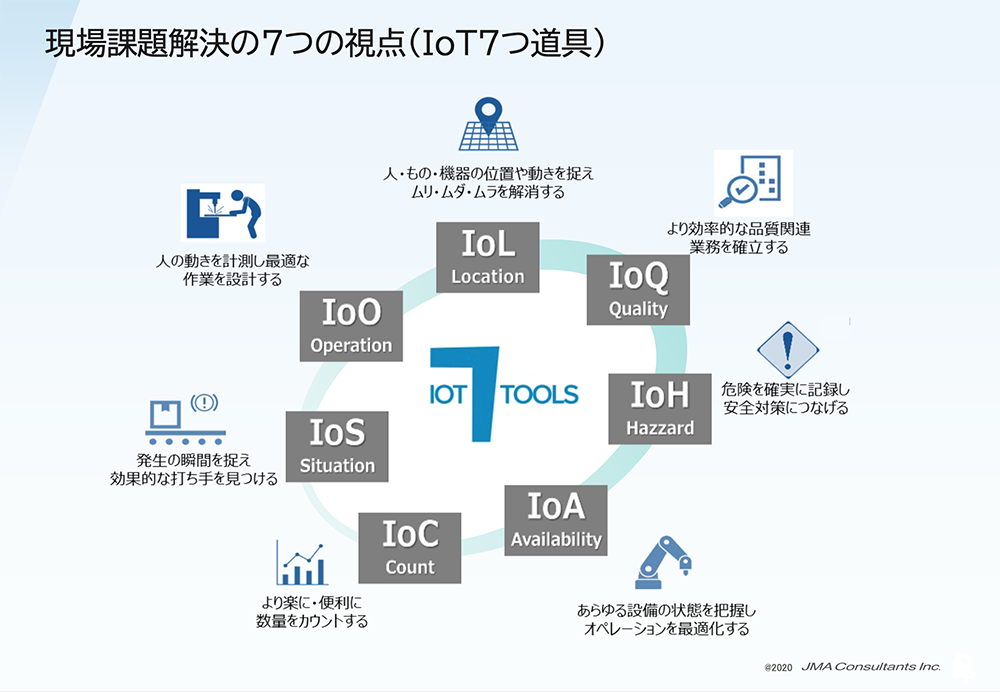
製造現場の課題や改善ポイントを発見するための7つの視点。JMACでは「IoT7つ道具」と呼んでいる
(図提供:JMAC)
「すべきこと」は製造工程以外も
見ないとわからない
本当に必要な「スマートものづくり」がどんなものかを考える際に、工場内のことだけを考えがちですが、それでは視野の狭いものになってしまい、失敗の可能性が高まります。顧客ニーズ、アフターサービス、設計・製造技術からの要請、供給・流通のサプライチェーンから見た必要性など様々な視点から考えてみることが必要です。その例として挙げられるのが、下記の「スマートファクトリーイメージセル」です。
こうしたものを参考にしながら、自分の会社にとって本当に必要なDX・スマート化がどんなものかをとことん考えていくといいでしょう。
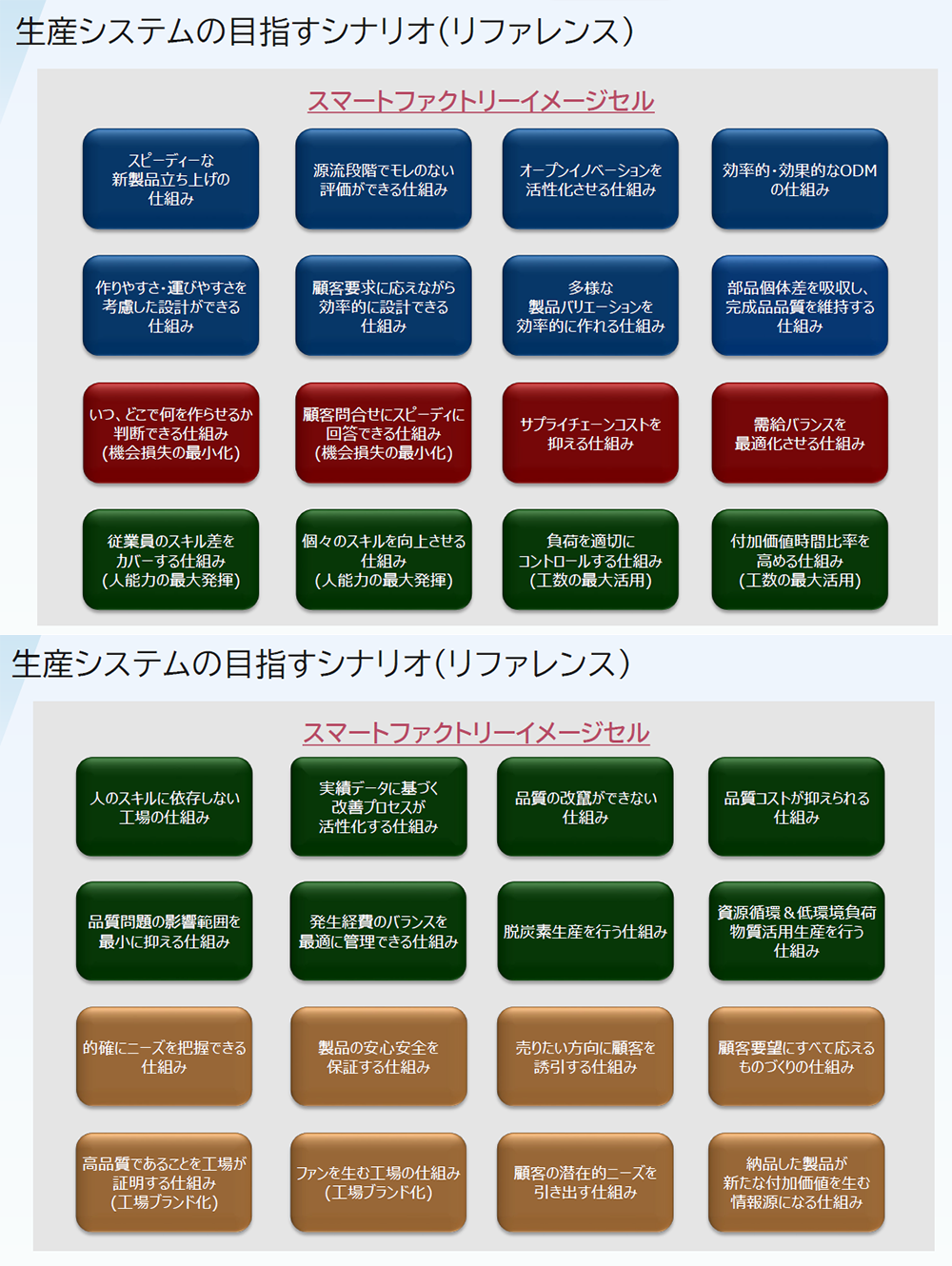
JMACでは「スマートファクトリーイメージセル」に基づいて、工場やサプライチェーンのスマート化をしようとする時に考えられるシナリオを32のパターンに整理している。自分の会社にとって本当に必要なスマートものづくりを考える時の参考になる。
(図提供:JMAC)
全社挙げてのプロジェクトとして
DX・スマート化に取り組むことが成功のカギ
最初はローコスト、スモールスタートで始めたDX・スマート化も、次第に本当に必要なことが見えてきたら、予算を改めて考えて、本当に必要なことの摺り合わせをしながら目指す方向を固めていきます。こうして、シナリオがしっかり固まったら、担当者やプロジェクトチームの組織を決めて、本格的に取り掛かることになります。
「スマートものづくり」を会社・工場全体で実現するためには、それなりの金額が必要になってくると覚悟が必要です。もちろん、金額は、企業規模、業種・業態、何をどんなレベルで実現しようとするか、どこまでを外注し、どこまでを社内でやるかなどによって大きく異なります。中小企業規模の工場においても工場全体をDX・スマート化をしようとすると補助金などの上限額である1000万円の壁はわりと早い段階で超えてしまうと思ったほうがいいでしょう。
投資金額はある程度大きくなる上に、スマートものづくりは、導入に成功したからといってなかなかすぐに利益を生み出すものではありません。多くの場合は、長期的に収益に寄与してくるものです。こう考えると、全社規模での取り組み、例えば1つの工場をスマートファクトリーに生まれ変わらせるような取り組みには、経営トップの強力なコミットメントが不可欠です。少なくとも、投資と人事の両面で意思決定できる経営メンバーが必要です。
もちろん、もっと規模の小さな現場レベルのDX・スマート化は、現場の方々がボトムアップでどんどん進めていくケースがあります。こちらについての予算規模は、製造業であれば一般的な改善活動にかかるものと同様のレベルだと考えていいでしょう。
補助金・助成金は
プラスアルファのカードと考えておく
中小のものづくり企業がDX・スマート化プロジェクトの予算を考える上で、ものづくりやIT・IoT導入のための補助金をどう組み込むかは重要です。
補助金の審査に通れば大きな力になりますので、どんな補助金があるかをしっかりと調べておくべきです。基本的には、「ものづくり・商業・サービス補助金」や「IT導入補助金」のような経済産業省、中小企業庁関連の補助金から調べていき、自社に該当するものを選んで応募するかどうかを検討しましょう。
政府の補助金以外にも、国立の研究所や学会による最新の知見が得られるワーキンググループの場や、地域ごとに様々な補助事業がありますので、こういったものについても探っておくと打つ手は広がります。
補助金や助成金について調べる際には、ノウハウやDX・スマート化のために必要な情報や知見を提供してくれたり、相談に乗ってもらえたりといったサービスも各地域でありますので、こういうサービスや拠点を利用するところから入るのも賢いやり方です。
人手が足りず日々の業務負荷が高くてできないという会社も多いかもしれませんが、情報収集の余裕があるのであれば、地域ごとに開かれているであろうDX・スマート化関連の勉強会やワーキンググループに参加をして、そこでネットワークを広げながら、どんな支援制度、補助制度が使えるのかを探っていくことです。そういう日々の情報収集を余念なくやっていくことが成功に近づく近道となります。
ツールありきの計画は失敗につながるという話と同様に、先に予算ありき、補助金ありきの計画立案も賢明なやり方ではありません。あくまでも会社としてやりたいこと、やるべきことが先にあり、そのためにいくら予算が必要で補助金の活用を考える。そうした手順で、スマートものづくり計画を進めていくべきでしょう。
公的機関による事業制度、支援制度の例
分野 | 事業制度や 支援制度の名称 |
提供機関 | URL |
---|---|---|---|
AI | 人工知能技術コンソーシアム | 国立研究開発法人 産業技術総合研究所 | |
ロボット | 賛助会員向けサービス | 一般社団法人 日本ロボット工業会 | |
ITツール全般 | 認定情報処理支援機関検索システム | スマートSMEセンター |
横スクロールできます
(監修:日本能率協会コンサルティング デジタルイノベーション事業本部 AI・IoT推進室 室長 小野甫、同社 デジタルイノベーション事業本部 スマートファクトリー推進室 室長 神山洋輔/構成・文:髙山和良)
三菱HCキャピタルでは、お客さまの事業をサポートさせていただく
様々なサービスを展開しております。